Our team successfully developed since many years the cloud based Supplier Portal.
First the functionality was mainly focused on Global Tools and Asset Management.
Afterwards Project Management, Follow-Up Reports, Supplier Quality Assurance, Initial Sample Process and Change Management features have been added step by step by a team of experts.
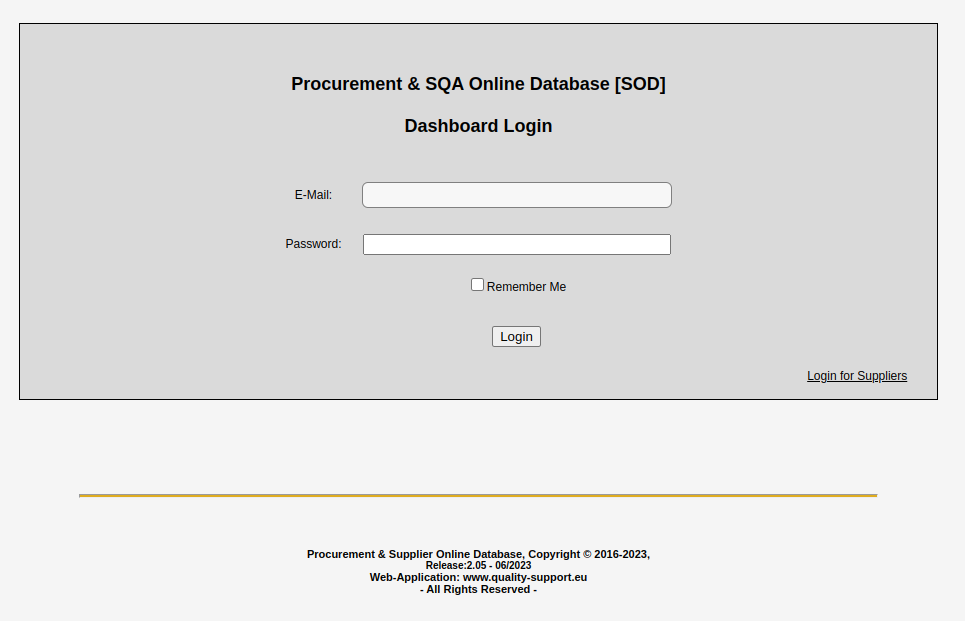
Today our cloud-based Procurement and Supply Chain Software provides on-demand connectivity to organizations and users around the world. It enhanced the Information flow and data Exchange with single sign-on and delegated administration and facilitates information exchange and collaboration tools.
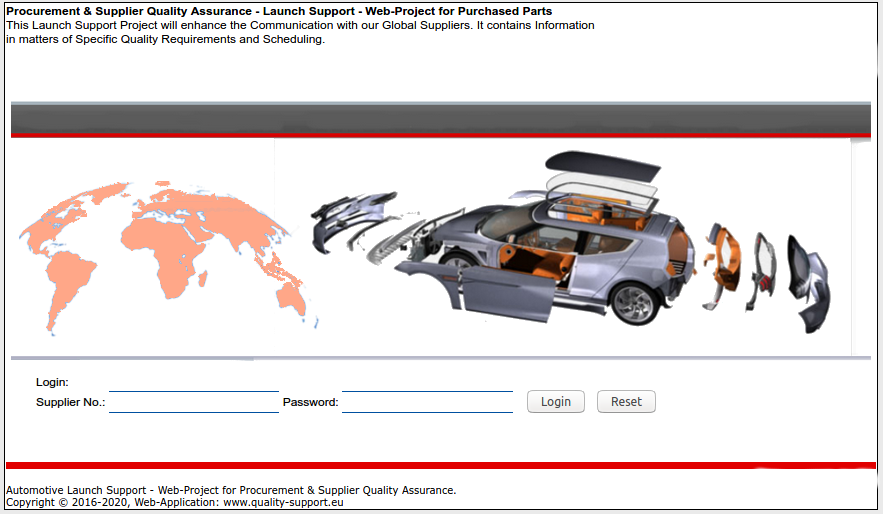
It provide shared data services for Vendors and a Dashboard to circulate project information through the whole corporation and external consultants.
Basic functions are:
- Suppliers:
Maintenance of all relevant Supplier data, Audit schedules and Quality Status information - Tools / fixed assets:
Management of all Production tools and peripheral equipment (fixed assets) (Transfer schedules, Home Line production status etc. - Components / Products
Products status data, technical change level, PPA quality release status, schedules and open tasks - Technical Change Management
Document control and tracking of technical changes and storage of related documents for circulation and reporting - Worldwide distribution of standards, schedules and forms.
- Interface for data import and export (Office or ERP Software)
- PPAP [PPA] Production Part Approval Process:
Target date tracking of all relevant PPA requirements and archieving of documents for circulation and reporting
PPAP document structure:
The abbreviation PPAP stands for Production Part Approval Process. The Production Part Approval Process is a structured sampling procedure for series production parts and spare parts, which was first defined in the automotive industry. The main purpose of PPAP is to assess the quality of the supplied parts to determine whether they meet the specified requirements, as well as to ascertain the extent to which the production processes ensure that these requirements are reliably met. PPAP is clearly structured and standardized according to the AIAG reference manual (Automotive Industry Action Group) and includes the basic requirements for the sampling of all your production and spare parts according to IATF 16949.
VDA’s Production Part Approval Process (PPA Procedure) is the German equivalent to the PPAP sampling procedure. As the procedures are very similar, we will handle the PPAP and PPA structure in the same way.
SUCCESSFUL PPAP USING THE RIGHT SOFTWARE
To achieve a structured Production Part Approval Process, it is recommended to support this process using a PPAP software solution.
The advantages of PPAP software at a glance:
- Centrally controlled production process and product approval processes from the perspective of the supplier, the manufacturer and the customer
- Simplified process to define characteristics and plan detailed reports
- Readings can be recorded, results communicated, and the documentation managed efficiently online
- Networked, standardized exchange of information between all those involved in the process
- Your approval processes are documented in line with IATF 16949, VDA 2, AIAG and DIN EN 9102
Our software solution offers all the above to support you in implementing a structured, efficient sampling procedure into your quality management processes – including re-sampling and requalification testing.
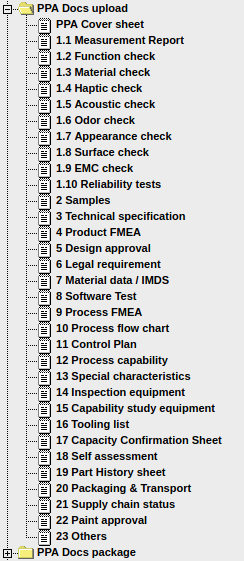
The software runs on standard Internet Browser’s and on Mobile Devices and it does not require any other add-on.
Do you like to improve the communication and accurateness of data excanche within your Supply Chain?
Do you have any questions on how to introduce a software solution to professionally manage your Supply Base and the Production Part Approval Process at your company? Or are you interested in training? Then please feel free to contact.
We have favorable licence fees.
Simon Krepler